Students
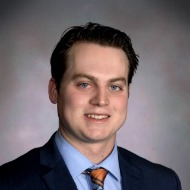
Jordan Fogarty
Economics, 2020
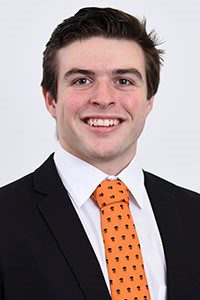
Joey Fallon
Economics, 2020
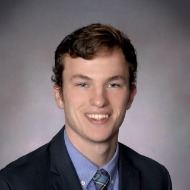
Jeremy Germain
Woodrow Wilson School, 2020
Project Description
For our EPICS project, we decided to make a birdhouse that is a tribute to the place on campus where we spend most of our time: Hobey Baker Rink. All three of us are members of the Men’s Varsity Hockey Team, and spend over 40 hours a week at Hobey skating, working out, relaxing and doing homework. It has essentially become our second dorm. Hobey Baker Rink is one of the most historic rinks in the world, and is the second oldest Division 1 rink in the NCAA, having been built in 1922. Our birdhouse is thus meant to roughly resemble Hobey while still serving as a functional birdhouse for birds of all sizes. In the first half of the year, we focused on building a stable birdhouse, while in the second half we focused on adding extra visually attractive and useful design elements, mostly through utilization of the Cameo machine and solar powered lights. Additionally, we designed our own gravity powered automatic bird feeder through the use of CAD software and 3D printing to feed the birds who call our birdhouse home. This bird feeder was placed on the back portion of the roof of the birdhouse, so that the birds could stand on the roof while eating. Further, to make this a sustainable birdhouse, we included solar powered lights make our project visible at night through green energy. Our birdhouse is made from spruce fir wood. In its construction, we utilized a variety of power, conventional tools, and automated tools, including CAD software, the X-Carve and Carvey, the Cameo machine, the belt sander, and the mechanical saw. We particularly enjoyed learning how to use the 3D printer, as it allowed us to design and create important part of our birdhouse, the bird feeder. We would like to thank James and Mauricio for all their guidance, as well as their patience, in instructing 3 non-engineering majors throughout the year. We hope you enjoy our Hobey Baker birdhouse!
Technical Background
Three-dimensional carving and printing allows inventors and fabricators to create new designs and implement them accurately and quickly. When manufacturing projects, people have gone through the process of using materials and cutting out what designs and features they want to have in them. Through this relatively new process of “additive manufacturing” fabricators can produce what they desire through layers of raw plastic material (Kurman and Lipson 11). This eliminates waste of raw materials while also providing near perfect accuracy to CAD mockups.
The ability to do both 3D carving and printing is due to the slightly older technology of “computer aided design” or CAD for short. This allows for prototypes and objects to be designed to precise dimensions in interfaces such as Fusion360, SketchUp and AutoCAD. Without these programs, additive manufacturing and 3D carving would be impossible. This is due to the computer software telling the printing machines exactly what to print, and the printers executing the orders from the software. Luckily the process of designing prototypes to be printed is becoming easier with more user friendly and intuitive programs. Currently, the computer usually tells the 3D printer what to print through G-Code production, however the EPICS lab is lucky enough to have a Zeus 3D printer that can do this on its own from the CAD files.
The applications and future outlook for these technologies is outstanding. First, by eliminating waste materials, factories will be able to reduce costs and space needed to manufacture prototypes, while also increasing output speed. Additionally, the materials formed by these machines use a honeycomb cell printing technique that produces extremely strong structures as they can “reduce the weight-strength relations” of what they are printing (Hernandez and Wong 5). While this is not quite applicable for large scale production, it is useful for prototypes and small replacement parts for machinery.
Lipson, Hod, and Melba Kurman. Fabricated: the New World of 3D Printing. John Wiley and Sons, 2013.
Wong, Kaufui V., and Aldo Hernandez. “A Review of Additive Manufacturing.” International Scholarly Research Network, vol. 2012, 17 June 2012, pp. 1–10., doi:10.5402/2012/208760.
Design Drawings
Fabrication Process
To create our birdhouse, we first examined Hobey Baker Rink both in person and through online pictures to come up with drawings that roughly modeled the rink. We could not find exact dimensions of Hobey Baker Rink through publicly available information, so we came up with a design that captured the spirit and essence of Hobey Baker Rink, even if not being exact in scale or design. To this end, when we brought our birdhouse to the rink, our rink manager immediately recognized it as Hobey Baker, even before we mentioned it was indeed supposed to be the rink. After completing the design, we worked on building the actual birdhouse. We cut multiple pieces of spruce fir wood to our specified dimensions using the mechanical saw, smoothing them out using the belt sander. We then created the design of the front of the birdhouse using the Carvey machine, which included a sizable door for many different types of birds to utilize. After that, we worked on designing and creating a bird feeder. We designed the bird feeder using CAD software/Sketchapp, a software that all three of us were fairly inexperienced in using. Mauricio was very helpful in teaching us how to use this software, and helping us get our design to a point where it could actually be fabricated. Once this design was ready, we fabricated the two separate pieces using the 3D printer. Because of the limitations in our design, we had to finalize the two pieces by using an x-acto knife, and joined these pieces together using gorilla glue. Once we had these elements fabricated, we worked on painting the birdhouse. We designed a block pattern for the sides of the birdhouse using the Cameo machine. Much like the actual rink, some of the blocks, which are meant to resemble stone, are more faded in color than some of the other block. In true Princeton fashion, we painted the sides of the rink black, and the top of the rink orange. After we were finished painting, we attached the bird feeder to the roof of the birdhouse using gorilla glue. As our final design element, we added solar powered lights around the roof of the birdhouse. These lights activate when it is dark and last for up to 10 hours on a single solar charge, allowing birds to utilize the birdhouse at all times of the day. We hope you enjoy our birdhouse!