Students
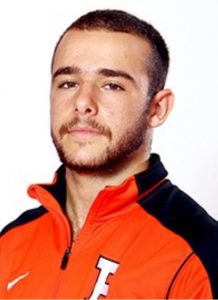
Leonard Merkin
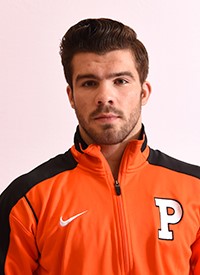
Matthew Kolodzik
Project Description
This impulse behind this project came from two things we love most: Music and Wrestling. Our project goal was to combine a wrestling headgear with Apple Airpods so that athletes can listen to their own music during practice and warm up. To do this, we aimed to place the Airpods in an encasement which could fit safely and securely inside of the headgear. The case needed to be non-intrusive, easily accessible, and sound amplifying. Plastic was the initial candidate; however, plastic is difficult to secure to the headgear shell, which has no flat surfaces for mounting. Additionally, had plastic was potentially hazardous due to its proximity to the ear. We considered a softer, more elastic material and came to two equally viable candidates: Silicone and the 3D Printing filament Thermoplastic Polyurethane (TPU), often referred to by its trade name, ‘Ninjaflex’. Lastly, we considered creating an injection molded silicone “sleeve” around the Airpods, however, designing and manufacturing with silicone proved slow, unwieldy, and unfavorable to modifications. TPU is extremely favorable in comparison to silicone injection molding. Its elasticity allows for easy adhesion to the inside of the headgear. This flexibility eliminates the need to secure the case via wire tethers or toleranced buttonholes, as was originally brainstormed. Most importantly, by using adhesive at the base of the flexible encasement, no design modifications are necessary for various brands of headgear and placement can be customized to the athlete’s preference. Ninjaflex proved to be perfectly suited to prototyping and fabrication, and we are extremely pleased with our final product.
Technical Background
3D printing starts with a digital design created on a computational CAD software. After modeling, a different software slices the object into thin layers which enables the printer to understand and interact with the object. 3D printing allows for rapid prototyping and material testing of 3D printable materials. One such material is Thermoplastic Polyurethane, or TPU, a 3D printing extrusion material that is both elastic and durable. Often referred to by its trade name, ‘Ninjaflex’, TPU is incredibly apt to rapid prototyping flexible products like phone cases and other impact resistant encasements. Unfortunately, there is a learning curve associated with printing flexible filament. Normally, 3D printers heat up and extrude hard plastic like PLA or ABS onto a print bed, which is also maintained at a high temperature. TPU requires an even higher extrusion temperature than both these plastics, and a low print bed temperature to ensure proper layer adhesion. Furthermore, an extremely low extrusion speed is used in keep filament from bunching up or clogging the extruder. Navigating these parameters requires lots of trial and error, as print profiles vary from machine to machine, however, once these parameters are discovered for any particular machine, TPU provides a wonderful, and flexible product.
Silicone molding was another method used to produce impact resistant cases and molds. Silicone usually comes in LSR (liquid) or HCR (pliable rubber) form. Like 3D Printing, both halves of a silicone mold are created in CAD software. When making a mold, it is important to pay close attention to how it will be removed after it has set. Improper decision making may lead to destruction of the part. The best method for HCR silicone is usually to slice it long ways in two halves, but this is not always possible. The mold may need to be played with until a suitable orientation and slicing is found. These techniques are good for prototypes; however, injection molding is usually done with LSR silicone. While Silicone Molding does not favor itself to rapid prototyping; it’s an incredibly efficient means of producing final products in large quantities.
No references “What Is 3D Printing? How Does a 3D Printer Work? Learn 3D Printing.” 3D Printing. Accessed March 14, 2019. https://3dprinting.com/what-is-3d-printing/#How-Does-3D-Printing-Work.
“Silicone Micro Molding, Manufacturing & Production | Albright Technologies.” Albright Technologies | Silicone Molding, Medical Silicone Prototyping, Injection Molding & More. Accessed March 14, 2019. https://albrightsilicone.com/silicone-micro-molding